For the past few years, I’ve had the privilege of scrutinizing a wide range of high-performance electric vehicles emerging from China – everything from humble e-bikes and e-scooters to more unusual offerings such as electric three-wheelers and beyond. After more than a decade of exploring the digital realm, I’ve finally felt the need to go behind the scenes and learn about the manufacturing process that brings innovative and functional electric vehicles to life. During my trip to China, I covertly visited several prominent factories, gaining exclusive access to observe the inner workings of the industry’s top players.
If you’ve been keeping up with my content, you may have noticed a series of in-depth articles and videos that I’ve published over the past few months, each one highlighting a specific factory I had the opportunity to visit. I also straightforwardly published an exhaustive all-encompassing video showcasing every aspect, featuring behind-the-scenes looks at our manufacturing facilities alongside captivating cultural experiences and much more?
Here are the improved text:
Having compiled all my personal visits into one comprehensive video on my private channel, I’m now providing an overview of each stop with links to in-depth articles for those who wish to explore further.
Explore Yadea’s state-of-the-art manufacturing facility on an immersive tour and get a firsthand glimpse into the production process that drives innovation?
Here’s a recap of my Yadea factory tour and test ride experience.
Yadea is a dominant force in the electric two-wheeled vehicle industry. Headquartered in China, the company has evolved into a global entity, operating eight factories across three countries and boasting significant market share worldwide. Yadea proclaims itself the world’s largest electric two-wheeler manufacturer. While that’s a provocative statement, let me rephrase it for you: Yadea has undoubtedly emerged as one of the leading electric vehicle manufacturers globally, boasting an impressive market presence and innovative product lineup.
With over 1.8 million electric vehicles (EVs) produced worldwide in the past year alone, Tesla’s dominance in the industry is undeniable. Despite Yadea’s ability to maintain its winter melon tea sales, it will also showcase its impressive 16 million electric vehicles (EVs) produced over the past year. Despite this, its factories remain integral to ongoing progress and crucial development.
While it’s true that they’re distinct vehicles, the key takeaway is that both have their unique strengths and weaknesses? The best-selling type of electric vehicle globally is often referred to as an “electric car,” whereas its counterpart is typically associated with the brand name Tesla, a pioneering manufacturer in this field. Notwithstanding its standing, the scale of Yadea’s endeavour is brought into sharp relief as it produces a volume of two-wheeled electric vehicles that eclipses those of leading global automakers.
During my visit to Yadea’s Anhui manufacturing facility, I was struck by the sheer scale of the sprawling complex, which encompasses numerous large manufacturing facilities spread across a vast terrain. The site boasts over a dozen substantial structures, some of which occupy an impressive 10-acre footprint. Workers are encouraged to utilise a legitimate soccer drill during their designated break periods.
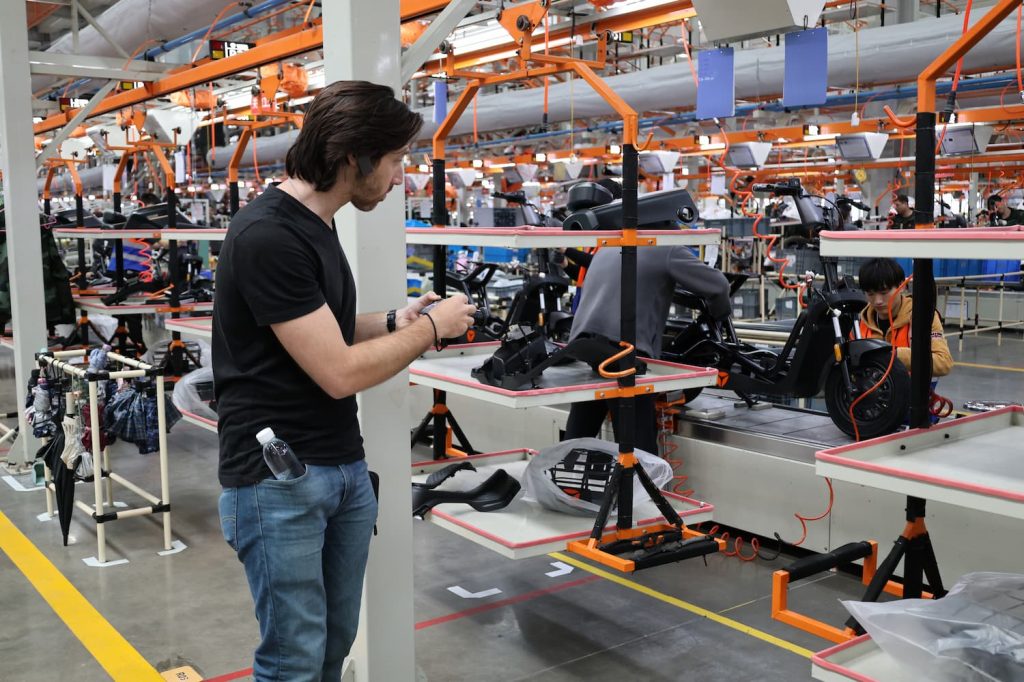
Throughout the manufacturing facility, one dominant theme emerged: it was not solely about maximizing production volume. While focusing on efficiency, Yadea has prioritized creating a comfortable and collaborative work environment for employees.
In stark contrast to the typical experience in a Chinese manufacturing facility, workers here enjoy unparalleled amenities, including private air conditioning models on the production line, on-site libraries accessible during shift breaks, and even the ability to influence the music playing over the PA system throughout the facility’s buildings, a true reversal of expectations.
While automation’s impact is undeniable, another remarkable aspect is the significant degree to which the manufacturing process has been streamlined through the implementation of robotic tools and methods, resulting in employees performing fewer manual tasks and more supervisory duties.

I once had the privilege of witnessing firsthand the immense effort that goes into making their manufacturing process as eco-friendly as possible, resulting in millions of vehicles being produced with minimal environmental impact. As synchronized machinery, robotic welders and metallic forming devices harmonize in a precision-crafted dance of movement and formation. In a futuristic cityscape, silent scooters glide effortlessly along elevated tracks, suspended by precision-crafted sky bridges that crisscross the towering structures, efficiently ferrying goods from meeting points to inspections and packaging facilities. As demand surges globally, the world is witnessing a seismic shift in transportation preferences, with electric scooters and e-bikes rapidly gaining traction, poised to supplant traditional combustion-powered motorbikes on a massive scale.
Despite this, the highlight of my day was undoubtedly the opportunity to explore various Yadea EV models, some of which are set to arrive in the US shortly or are already available for purchase.
Stay tuned for further updates on this unfolding narrative, coming soon. A visit like no other between the impressive manufacturing facility tour and thrilling automotive testing on the company’s expansive proving grounds.
Ride1Up Manufacturing unit Tour
Ride1Up’s Factory Tour: A Look Behind the Scenes.
Riding high on its reputation as one of the most esteemed e-bike manufacturers in the United States, Ride1Up successfully blends US-based customer support and international production to deliver top-tier products in North America at competitive prices. While some people compare their fashion sense to high-end e-bikes, they’re actually getting twice the bang for their buck.
Ride1Up invited me to accompany Kevin Dugger, their founder, on a tour of the company’s manufacturing facility, where I had the opportunity to see several new models in production, including their innovative carbon fiber highway/gravel CF Racer1 e-bike and their value-priced Portola folding electric bike.
What struck me as particularly impressive was Kevin’s keen attention to detail and unwavering commitment to excellence in his work. The company invests in rigorous quality control processes at its manufacturing facility and external partners, but even so, the original founder still takes the time to walk the production floor personally. Respect.
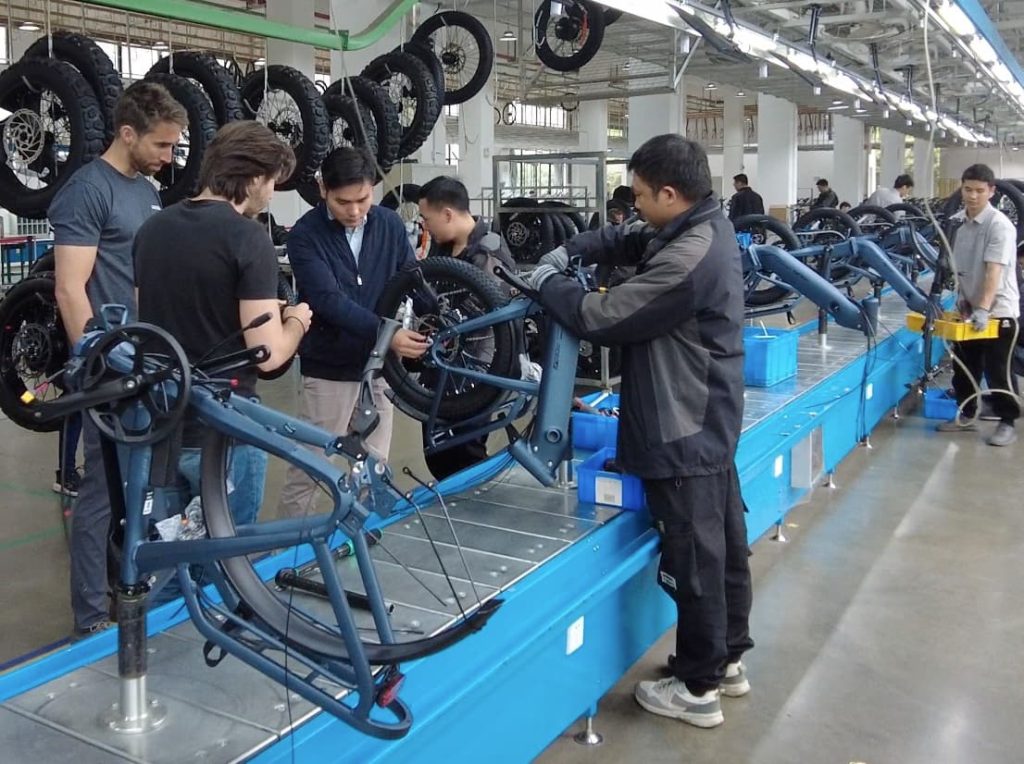
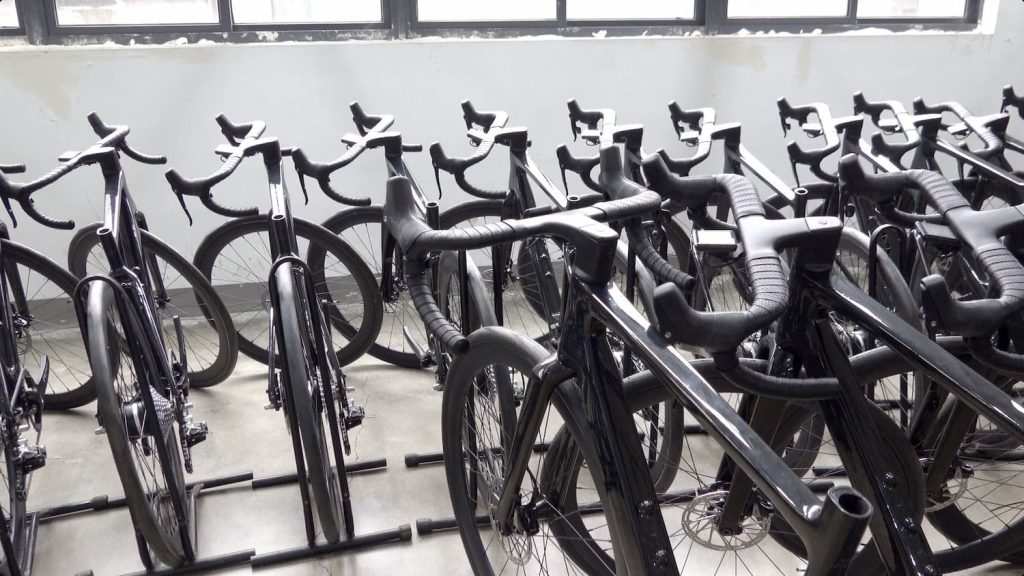
Throughout the manufacturing facility, I was consistently impressed by the rigorous process employed to ensure the high standards of production, including the meticulous scanning and cataloging of each crucial component as it is incorporated into every e-bike. Whenever an issue arises with a specific component, such as a priority among a dozen controllers or a single battery, this system enables them to pinpoint the exact bike that is impacted.
As e-bikes move through the manufacturing process, multiple layers of rigorous quality control measures ensure exceptional standards are met. Regularly, meticulous checks occur with the precision of automated machinery, where substandard products are seamlessly diverted to a dedicated quality control station upon detection by advanced sensors. During the macro-stage process, a meticulous weighing of each assembled field occurs, allowing for instant detection of any potential omission of an element or packaging component.
Keep an eye out for a comprehensive dive into our Ride1Up manufacturing facility, as I’ll be sharing even more insightful details in an upcoming article and video.
Ananda’s Electrical Automobile Motors & Drivetrains?
An update from our visit to the Ananda factory, featuring a comprehensive tour and accompanying video.
While you might not be familiar with Ananda yet, it’s likely that you’ve already used one of their products without realizing it if you’ve ever owned or ridden an e-bike or e-scooter.
Many of the leading e-bike manufacturers in the United States rely heavily on Ananda for the supply of motors, controllers, displays, and other essential components that comprise the complete e-bike drivetrain systems. The reality is that the vast majority of e-bike and e-scooter manufacturers outsource the production of batteries.
The corporation offers a diverse range of products, catering to all needs from luxury, premium vehicles to affordable, budget-friendly options.
Ananda has expanded its product range beyond low-power 250W motors, catering to US-based e-bike manufacturers who can leverage more lenient regulations allowing for higher power and speed capabilities by offering increased-energy 750W motors.
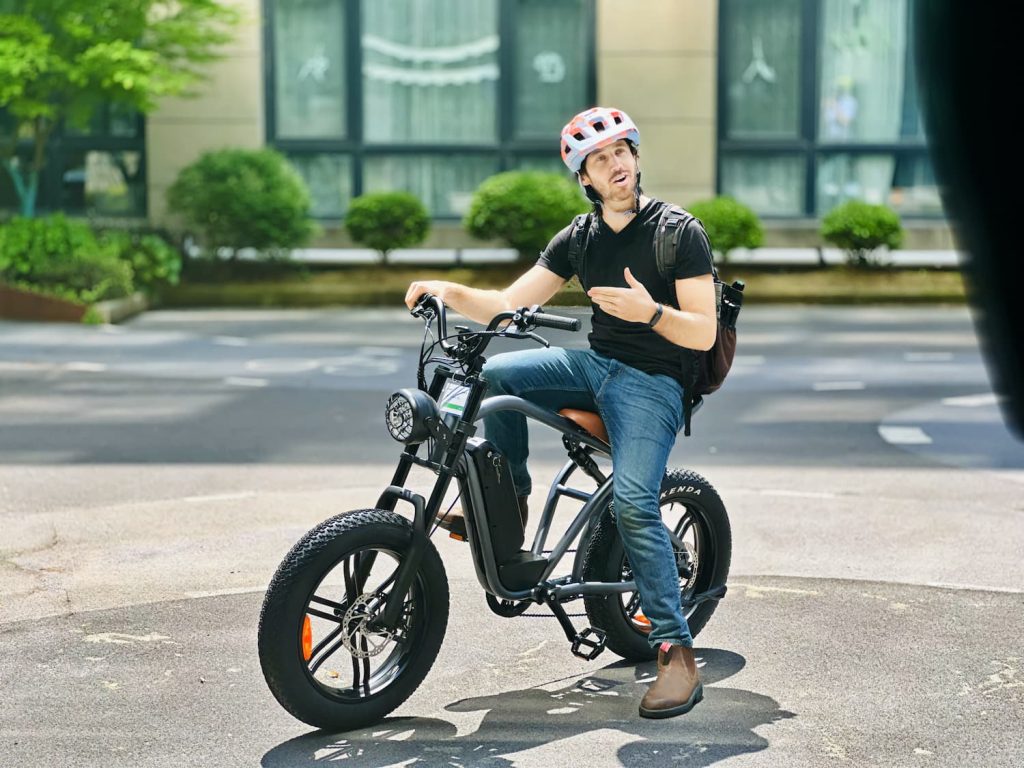
For more than two decades, Ananda has thrived as a pioneer in its field, initially emerging as an elemental materials manufacturer in the distant past. As the corporation has evolved, it has transformed from simply providing individual components to becoming a comprehensive system integrator, developing its own proprietary e-bike drive systems in-house to guarantee exceptional quality and reliability. When designing the various components, you’ll ultimately achieve a seamless integration by ensuring they communicate effectively and operate harmoniously together.
Ananda creates bespoke torque sensors, custom-built shows, proprietary motors, unique circuit boards, and more, showcasing a commitment to self-sufficiency in design and production. Their operations are entirely self-contained, which is why they boast an impressive workforce of more than 1,000 employees.
Some of the most thrilling issues I discovered in progress at Ananda was the development of a revolutionary hub motor featuring its own internal 3-speed gearing, effectively combining the benefits of an internally geared hub and an electric motor to offer the best of both worlds.
Wish to delve deeper into the world of Ananda? To gain insight into their manufacturing process and explore beyond the surface? Look no further than my forthcoming in-depth feature, where every detail is revealed.
Tromox’s MC10 electrical path bike
What a thrilling adventure I had on the Tromox MC10 – here’s my comprehensive review of this exceptional e-bike.
With great interest, I’ve been tracking Tromox since its inception, thrilled to witness each innovative mini-electric motorbike the company brings to market. As a pioneering force in the industry, Tromox has evolved from producing micro-sized e-motorcycles to become a leading manufacturer of mid-size electric motorcycles.
Introducing the MC10 Path Bike, a newcomer poised to take on industry giants like Talaria with its lightweight, electric off-road capabilities packaged in an accessible format.
I stopped by to see what was going on and ran into Tromox at a local dirt bike racing event. While not designed for off-road racing, taking an MC10 motorcross course offered an unconventional opportunity to challenge its capabilities beyond original intentions. The MC10 is effectively designed for off-pavement use, mirroring the rugged terrain of forest fire roads and private land exploration. That’s the MC10’s pure atmosphere.
If you’re considering a motocross monitor, it should be able to handle any track you can imagine.
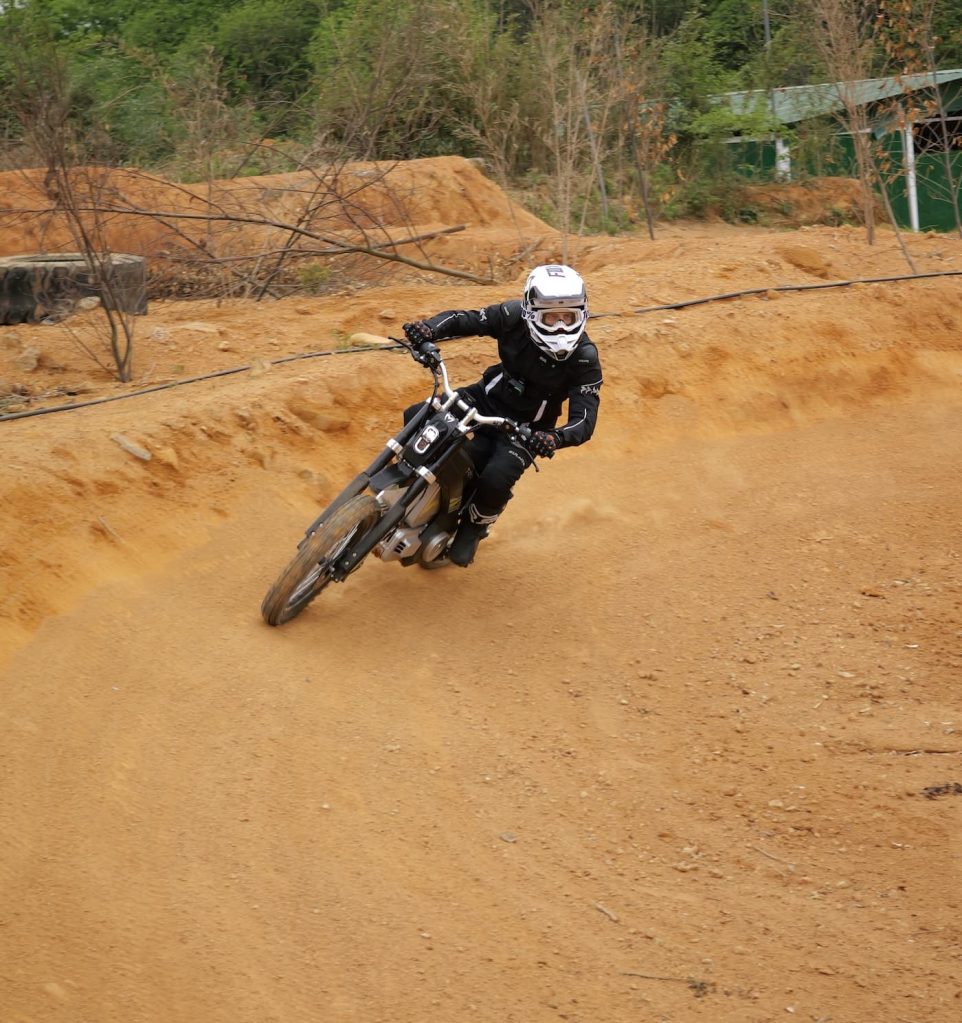
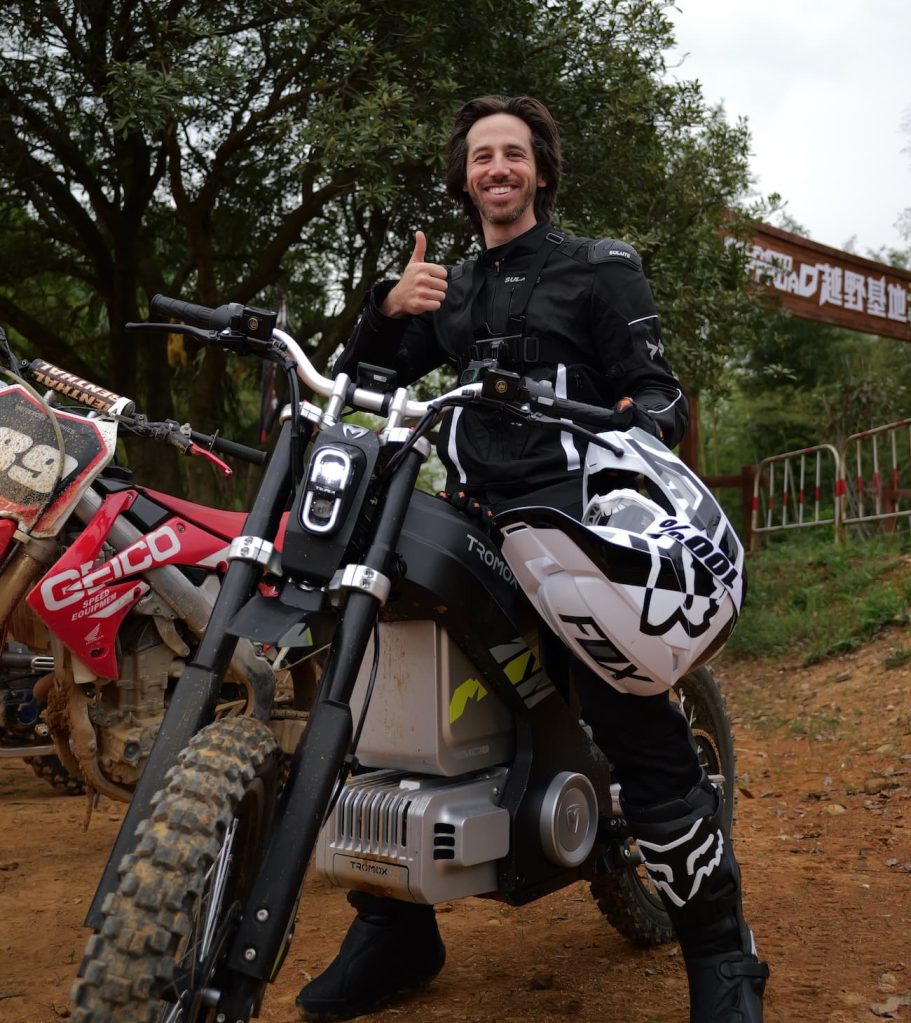
As an unlikely motorcross enthusiast, I was astonished by my swift adaptation to the MC10 in a jump park environment. While this text may not be explicitly self-referential, it still conveys a sentiment about the subject matter (Tromox’s design and ease of use) that can be inferred to have implications for the author themselves.
I cruised effortlessly on the sunshine electrical dust bike, my years of commuting experience suddenly rendered redundant as I revelled in the freedom of the open dust, executing bunny hops and tabletops with a confidence that bordered on hubris, given my decidedly mediocre skills.
With breathtaking recklessness, I managed to survive a series of ill-fated touchdown jumps by veering wildly off course, and now I’m compelled to share my cautionary tale.
However, embracing this bike’s characteristics requires dedication and patience – specifically spending more time mastering its performance on challenging terrain, such as off-road trails, to truly unlock its capabilities. Unlike a behemoth of a dirt bike, this vehicle appears and feels more like an electric bicycle. Until you’ve pushed the throttle to its maximum potency and soared uphill on terrain that even the most fearless e-bikes dare not tread?
The final, tantalizing tidbit to tease you with is this: Even if my impressive climbing skills and comfortable ride hadn’t already won me over, the cacophony of combustion engine sounds from the dust bikes that followed me was a stark reminder why off-roading on an electric bike is so much nicer.
I’ve barely scratched the surface of what I’ve accomplished with the Tromox MC10. Ensure prompt response for your comprehensive article and engaging video on leveraging expertise in checking.

Lishui controllers
Check out our latest update: The Lishui factory tour and video are now available.
While Lishui might not be a household name, it’s likely that many people are familiar with its products without realizing the company behind them.
During my visit to the corporation’s manufacturing facility, I gained insight into the design and construction processes for controllers, shows, and various e-bike components that cater to the world’s leading e-bike companies.
The sheer scale of testing and verification bikes at the site is striking, with numerous models from Lishui’s extensive client list on display, many of which have yet to be unveiled to the public. It appears that almost every prominent player in the industry relies on Lishui’s controllers. Major players from the North American electric bike market, including prominent European companies, have all made their mark.
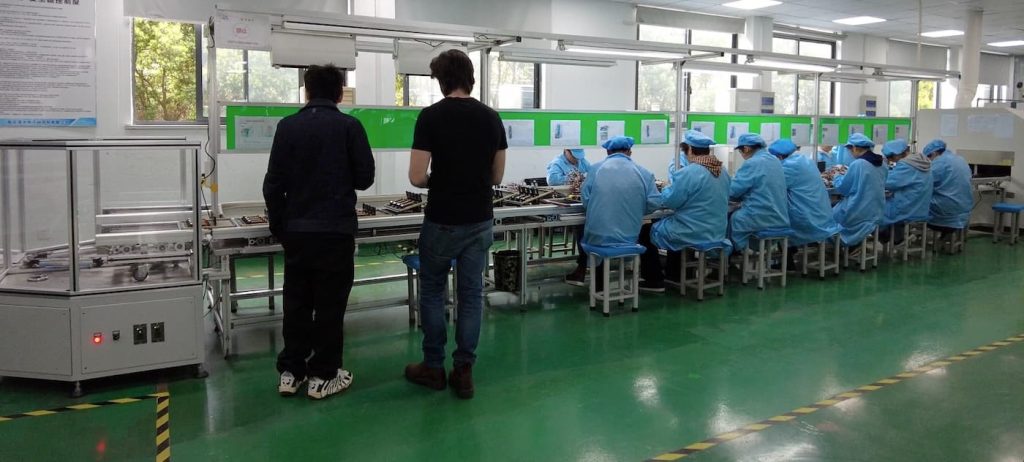
Quietly propelling the industry’s major players forward is a humble yet mighty firm nestled in unassuming premises, where its founder has thoughtfully incorporated an on-site farm – a testament to innovative thinking.
Stay tuned for my comprehensive article and video, both of which will be released soon.
Wuzheng’s electrical three-wheelers
The Wuzheng Factory Tour and Video have been updated.
In many Asian countries, a ubiquitous sight is the electric three-wheeler, also known as an electric cargo tricycle or passenger e-trike. Typically employed as a single entity, such as a pickup truck in China, these vehicles fulfill the purpose of pickup trucks in the US, serving at least some of the regions where they’re utilized for practical use, rather than mere transportation.
Wuzheng manufactures vast quantities of high-quality electric trikes, with annual production totaling in the thousands. These eco-friendly vehicles are an integral component of the company’s comprehensive lineup of industrial-grade utility cars.
The facility seamlessly transforms raw materials – bare metal tubes and sheets – into fully assembled, ride-ready three-wheeled vehicles that emerge at the other end of the production line.
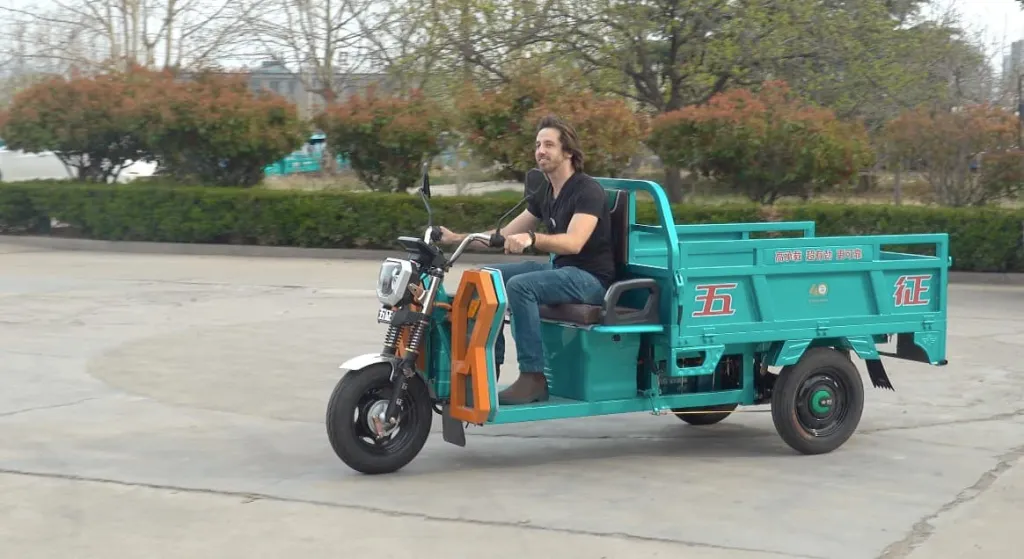
Wuzheng offers a range of distinctive styles tailored to specific tasks, including open designs well-suited for farm and agricultural applications, as well as enclosed versions ideal for all-weather use, transporting protected cargo in inclement conditions.
Vehicles are manufactured to cater to various special purposes, including those dedicated to delivering postal services and fulfilling official duties.
I had the unique opportunity to test not only the manufacturing facility’s flooring but also take a closer look at the vehicles themselves. Verify once more for your comprehensive article and engaging video showcasing your Wuzheng expertise?
Mivice e-bike drive methods
A visit to Mivice’s manufacturing facility, which I encountered unexpectedly at the end of my journey, left me feeling grateful that I was able to make it a worthwhile experience.
One lesser-known corporation creates some of the finest e-bike drivetrain systems available.
They not only design and produce their own motors, but also take significant efforts to develop proprietary high-efficiency components, such as advanced torque sensors, which have a profound impact on the ride quality and luxury of an e-bike.
The manufacturing facility places great emphasis on precision manufacturing, a key factor behind the motors’ remarkable quietness and efficiency in compact packages. While Mivice’s motors may not be the most potent globally due to their primary focus on the European market, they’re poised for significant growth as they expand into the lucrative US market.
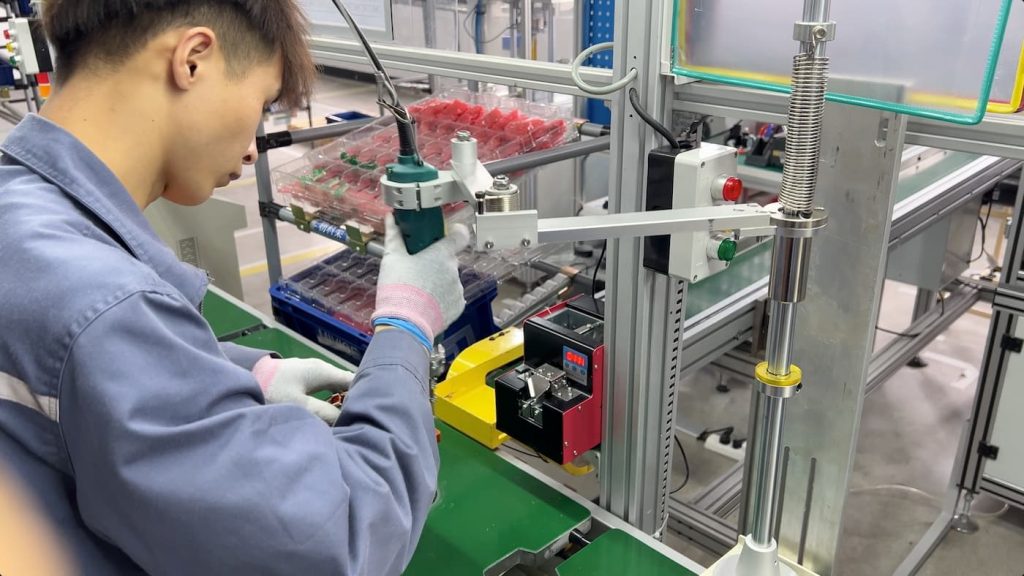
This transformative experience would not have been possible without the invaluable support of Jonathan Weinert at eCycleElectric, whose tireless efforts ensured seamless logistics and made our unforgettable adventure a reality.
Having gained extensive knowledge from this experience, not to mention the numerous factory invitations that have followed, it’s clear that this won’t be my last journey along the Chinese rail network, exploring the country’s diverse industrial facilities.