During my recent trip to China, I endeavored to explore firsthand how many of the e-bike drive systems and components commonly utilized in Western society originated and were manufactured. With a visit to Ananda, a leading and renowned Original Equipment Manufacturer (OEM), any exploration into the roots of premium e-bike components would be incomplete without this key stop.
I used to be in a position to go to the corporate’s R&D headquarters in Shanghai in addition to one in every of their manufacturing unit places in Wuxi, giving me a detailed take a look at the design course of and the way these designs get manufactured into actual e-bike programs.
Since commencing operations in 2001, Ananda has focused exclusively on micromobility initiatives since shifting its primary focus to this area in 2011. Since 2017, they have successfully developed a wide range of hub motors for e-bikes and scooters, and further ventured into manufacturing their own mid-drive electric bike motors. Since then, the corporation’s scale has experienced a significant and substantial growth.
While you might not be familiar with this corporation, it’s primarily due to their minimal marketing efforts; however, many leading e-bike manufacturers rely on their proprietary motors, controllers, and other components without openly acknowledging the partnership. To put these issues into perspective, the company manufactured roughly 6.5 million electric motors last year. While most of their merchandise were designed for the vast domestic market, around 600,000 units were exported to Europe and North America, where they gained a foothold in the e-bike industry. Many of the world’s leading manufacturers rely heavily on their software solutions. You may well possess an Ananda motor, controller, or other hardware in your storage at present, without being aware of it.
Ananda’s growth trajectory continues to soar, with a brand-new Vietnamese manufacturing facility currently in development. However, due to unprecedented demand in North America and Europe, the company is focused on establishing a new European manufacturing unit to meet this surging demand. Ananda has recently launched its inaugural North American service centre in Los Angeles, with plans to expand its locally based workforce in the United States.
As the primary designer and producer of almost every component used in an electrical bicycle, excluding batteries and BMS (Battery Management System), Ananda bears full responsibility for their creation. Notwithstanding, they collaborate with multiple battery manufacturers to provide rigorous testing that certifies the compatibility of these power sources with their comprehensive drive system portfolio.
Their core competence lies in analysis and improvement, with a focus on manufacturing implementation. While some companies simply manufacture elements designed by others or operate as contract manufacturers for third-party designs, Ananda takes a unique approach, offering an end-to-end solution that encompasses the entire production process, from design to delivery, with expertise spanning entry-level to high-end solutions.
While initially focused on part manufacturing, delivering proprietary motors and controllers, Ananda has evolved to become a comprehensive systems integrator. Many e-bike manufacturers receive a comprehensive e-bike system from us, excluding the battery.
With a single, all-encompassing strategy, the corporation has required an immense infrastructure, boasting over 1,000 employees and more than 200 automated machines – a significant proportion of which, 70 machines, is dedicated solely to automated coil winding.
Ananda is emerging as a key player in China’s mid-drive motor industry, expanding its product line to include higher-powered models designed specifically for the North American market. Given the need for seamless integration, our team has taken care to ensure that all North American-motored engines we design are compatible with throttle controls. Discuss figuring out your viewers!

Touring Ananda’s R&D facility in Shanghai
My tour at Ananda began within the R&D middle. The corporation boasts a talented team of engineers and designers dedicated to every facet of its e-bike drive systems.
A pivotal aspect of the design and development process is ensuring each component can withstand the rigors of daily usage in the extreme environments typically encountered by e-bikes and e-scooters.
I strolled past rows of machinery humming along, each one inflicting its own brand of torment – what would you suppose is going through your mind? Motor components are subjected to thermal stress when exposed to extreme temperatures, whether high or low. Tanks equipped with engines undergo rigorous humidity testing, oscillating seamlessly between damp and dry environments. The rain machines had worked tirelessly, delivering a ceaseless barrage of water upon the parched earth. Each machine looked increasingly unreliable, prompting me to think twice before risking my e-bike’s safety nearby.
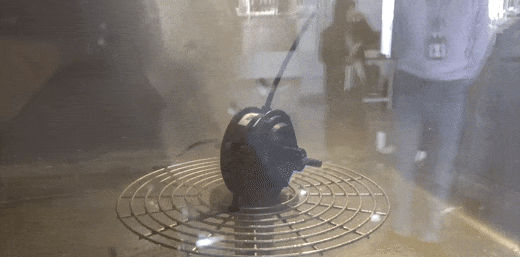
Robots have repeatedly pushed buttons on handlebars countless times, logging tens of thousands of instances. Motors were subjected to aggressive shock-loading simulations, mimicking the stresses of sudden stops and prolonged braking. Imagine a wayward broomstick jamming between the spokes, effectively grinding the motor to an abrupt halt.
Scores of dynamometers have been meticulously arranged for extensive, long-term testing, executing months of rigorous evaluation on perpetually operating motors.
Thousands of miles of rigorous testing had been conducted on entire fleets of e-bikes, utilizing advanced simulators that mimicked the demands of long-term use and extreme mileage accumulation.

In different elements of the R&D middle, banks of 3D printers whirred away, producing prototypes that will turn into fully new drive programs. A novel electric bicycle innovation is currently under development, which involves an integrated hub motor with a built-in three-gear transmission. A revolutionary fusion is poised to materialize, combining the potency of hub motors with the ingenuity of internally geared hubs, yielding a synergy that surpasses the sum of its parts.
In contrast to the cutting-edge technology that fills the machine shop, a rich legacy of traditional craftsmanship flourishes alongside, delivering essential precision-machining services for refining innovative designs.
Professional motorcycle mechanics establish rigorous testing protocols for mule bikes, while rider assessment teams subject them to extensive on-road validation.
After purchasing the system, I decided to don my thinking cap and test out several of the innovative motors and driving programs developed by Ananda. I successfully tested an M100 mid-drive motor that provided the perfect balance between stability, energy, and luxury, accompanied by a highly effective 750W M6100 mid-drive motor that was enjoyable but ultimately delivered more power than I needed most of the time. This innovative mannequin is poised to capture the hearts of American consumers seeking a high-performance ride that prioritizes both speed and style.
During my investigation, I scrutinized a moped-inspired hub motor setup, boasting forged wheels and an intricately designed drive system that seemingly incorporated a torque sensor, which accounted for its remarkably responsive pedal assistance. Only after a thorough examination did I discover that it was genuinely an exceptionally well-engineered cadence sensor, one that had successfully minimized pedal lag to almost imperceptible levels.
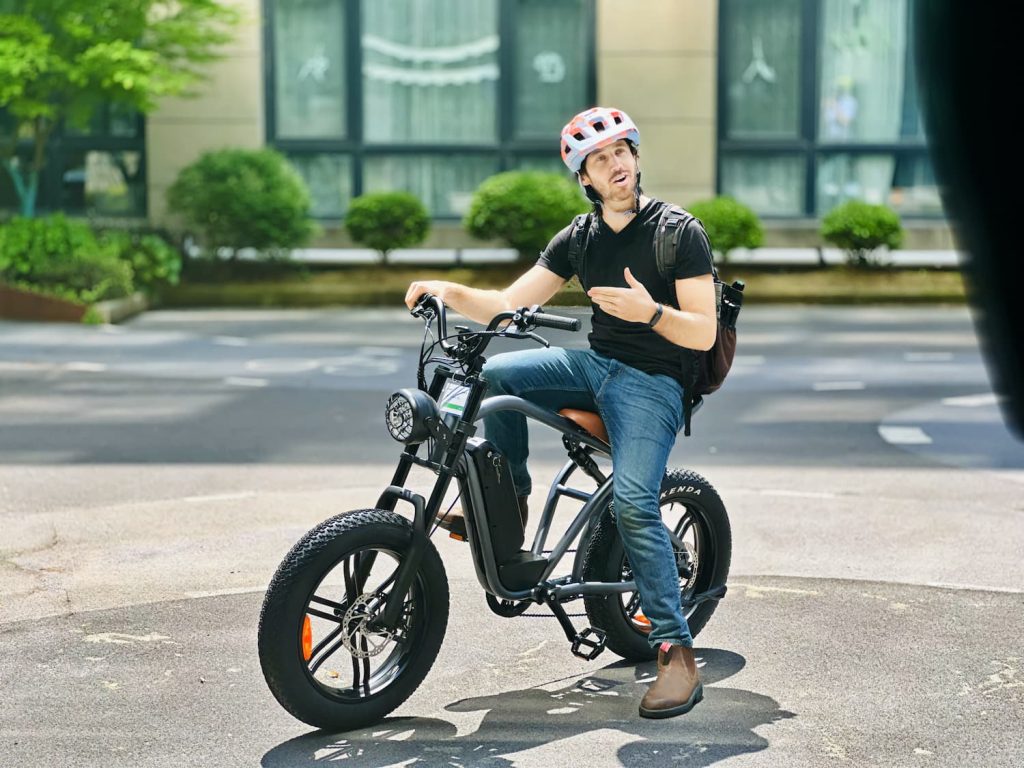
After rigorous testing of our e-bikes, we received confirmation on their latest diagnostic instruments, boasting advanced software that efficiently detects potential issues arising from extensive use throughout the product’s lifespan? Rather than receiving vague error messages, companies can simply leverage software to conduct diagnostic tests on bicycles, pinpointing the root cause of specific issues.
Ananda’s manufacturing facility in Wuxi
During the latter part of the day, I had the opportunity to visit one of Ananda’s facilities and witness their production process up close.
The initial step involves a meticulous examination and assessment of the components procured by Ananda from its vendors. Staff meticulously scrutinize each component down to the minute detail, ensuring a flawless production that meets exact specifications. A slight misalignment in the motor casing could potentially cause increased vibrations and premature wear.
The pinnacle of quality control lies in that meticulous stage of precision inspection, where discerning manufacturers recognize the paramount importance of unwavering accuracy to consistently deliver reliable products of unimpeachable excellence.
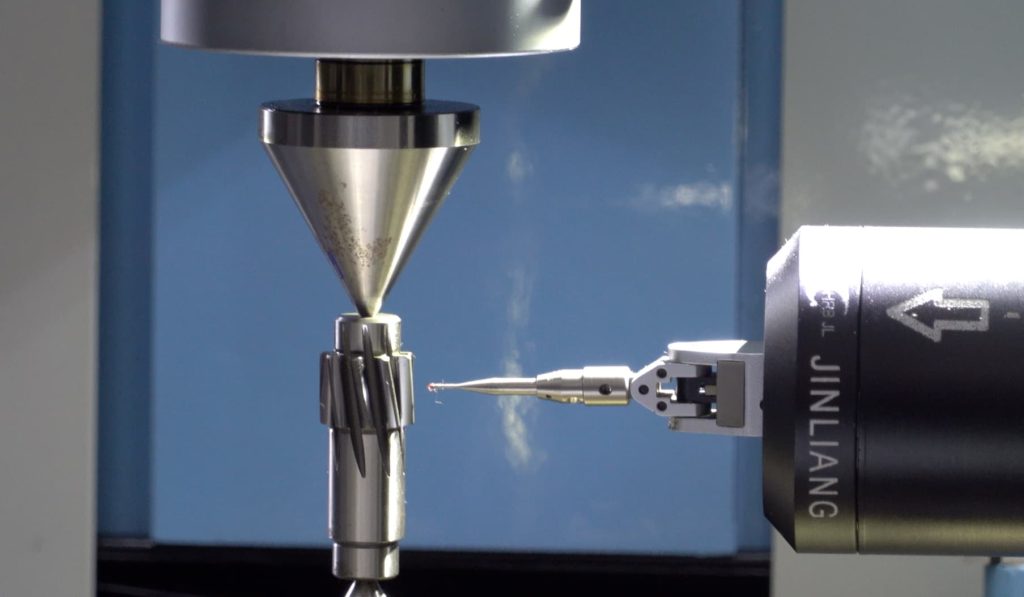
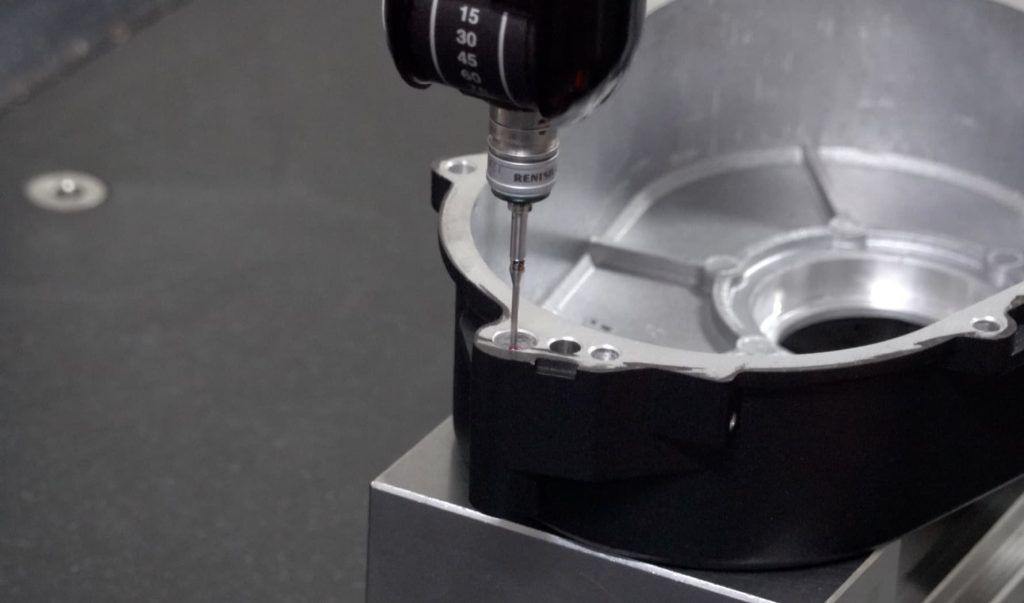
Upon arriving at the manufacturing unit’s grounds, we proceeded to the area where motors were being produced. The initial step involves a meticulous process of winding motor cores with copper wire, where precision-spun copper threads are carefully coiled across the motor’s stationary components.
In bygone eras, when electrical motors were still being assembled, it’s likely that those who have witnessed the process have come across images or films of women intently focused on their workstations, deftly winding motors with precision and care. With more than 70 automated motor winding machines at his disposal, the sheer scale of Ananda’s operation is a significant departure from its earlier state.
While modern manufacturing processes enable motor cores to be wound without direct human intervention, they are also produced with greater precision and consistency than ever before. One of the most impressive aspects of robotics is their capacity to operate with unwavering precision, never faltering or losing efficiency due to fatigue, as each motor is wound in a consistent manner every time.
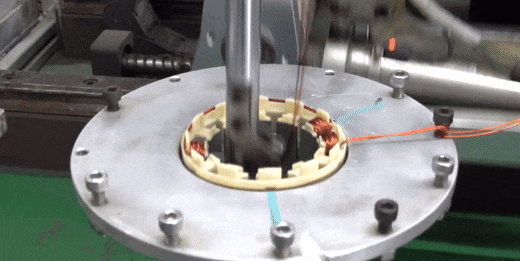
The wound motor cores are thoroughly inspected prior to proceeding with the next stage of assembly within motor housings. The meeting’s course is a blend of guided and autonomous responsibilities. Robotic assembly machines efficiently execute precision-intensive tasks, such as inserting gears and building internal transmissions.
The sub-assemblies are subsequently transferred to the balance of the production line, where they are manually integrated with the motor components. A laser engraver serializes each motor shell along its production route, before moving on to rigorous sound-testing procedures to ensure the component powers up and operates at a whisper-quiet level as intended.
Motors are often assembled using automated equipment, ensuring precise placement of motor gears and components.
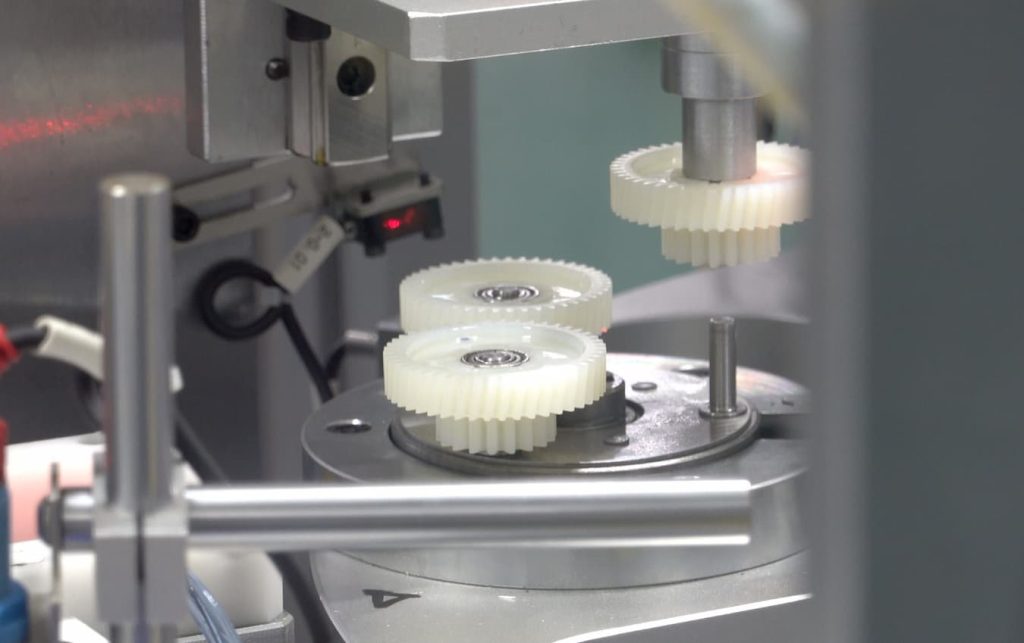
After every motor is fully assembled and tested, it’s digitally scanned and uploaded to our database before being carefully packaged for shipment to original equipment manufacturers (OEMs) who can then integrate them into a wide range of electric vehicles, including e-bikes, e-scooters, and e-mopeds. In the past, e-bike motors were typically shipped in foam packaging to protect them during transit. Ananda has made the switch to environmentally accountable paperboard packaging, ensuring equal safety without relying on hazardous materials that cannot biodegrade.
Apparently, in one other a part of the manufacturing unit, I noticed most of the identical torture testing machines that I had first seen within the R&D middle again in Shanghai. However, as I shortly understood, this was actually part of the standard management curriculum? In Shanghai, cutting-edge designs undergo rigorous examination during the development process; meanwhile, the manufacturing facility conducts comprehensive testing as part of regular inspections for each batch of components produced. To guarantee the motors meet performance expectations, rigorous testing procedures are employed, involving endurance tests under various load conditions and accelerated lifespan simulations, allowing for the detection of even minute variations between distinct manufacturing batches.
The purpose of this visit was to gain insight into the manufacturing process of controllers, which entailed suiting up and entering the company’s clean room facility for observation. There, automated choose-and-place machines constructed circuit boards that were then processed through multiple soldering machines to assemble the circuits. Using high-precision 3D optical imaging, the method’s efficacy is thoroughly monitored, enabling inspectors to scrutinize each solder joint from multiple perspectives and ensure that all components are securely attached to the circuit board with precision. By utilizing high-magnification imaging and evaluation techniques, companies can ensure that even the smallest components are properly positioned and soldered to withstand rigorous testing over an extended period of time, eliminating any potential defects or malfunctions that may arise thousands of miles down the road.
Conformal coatings are applied to electronics, forming a waterproof barrier that prevents corrosive water vapour from compromising metal and circuit integrity.
Each step within these processes is a vital and integral component of the manufacturing procedure, ensuring that products manufactured in Ananda’s facilities consistently meet their intended specifications throughout an entire product lifecycle.
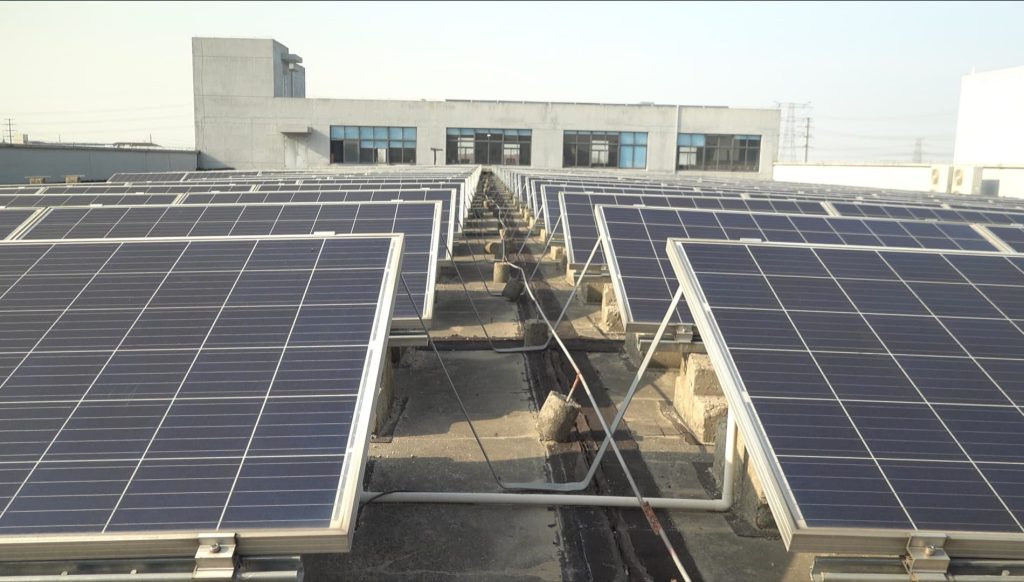
Rooftop photo voltaic array
The culmination of the tour was a moment that left me utterly astonished. Before departing the manufacturing facility, I was escorted up to the rooftop where a substantial solar panel array generated a significant portion of the energy used by the facility.
While not covering 100% of the company’s energy consumption, this initiative still makes a substantial impact and reinforces the crucial role that sustainable energy practices play in mitigating environmental effects, as exemplified by Ananda’s electric vehicle components.
Most of these steps extend a long way in reducing our personal hazardous impacts on the planet. Residents are constantly required to navigate their urban environments on foot, and leveraging two-wheeled electric vehicles stands out as a remarkably efficient means of accomplishing this daily task. If firms can fully offset the emissions generated by producing these vehicles, the benefits will be even greater.
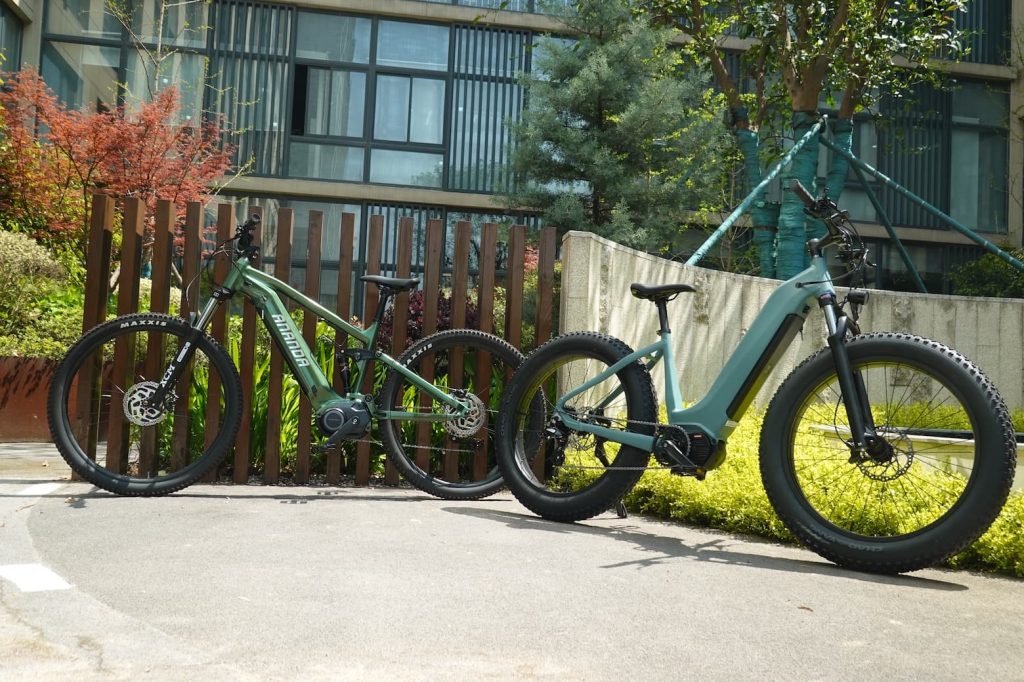
The takeaway
For years, I’ve been familiar with Ananda’s innovative electrical motors; in fact, I built some of my initial e-bikes using theirs over a decade ago. I was unaware of the massive scale to which Ananda has expanded its e-bike production system, leaving me wondering about their capabilities.
Removed from a single competitor, Ananda is a comprehensive system integrator by design. Established as a trailblazer in the burgeoning micromobility sector, Ananda has diversified its product portfolio to include everything from e-bikes and scooters to controllers and motors of various types.
Without meticulous attention to detail in manufacturing processes, it’s unlikely that companies would produce 10 million motors within a year, let alone millions of additional components, such as controllers, without learning something about the significance of quality control.
The corporation has effectively capitalised on its research efforts, developing a cutting-edge and highly mechanized design and production system that has evolved into a substantial operation.