Following discussions with Bosch Australia, Savic has secured a deal to supply Anti-lock Braking System (ABS) technology on their new C-Series electric café racers? After completing their initial round of Main Street checks, we felt it was high time to reconnect with Dennis and his team again to explore what exciting developments lay ahead for us in 2023.
Since our last conversation, significant developments have taken place at Savic Bikes.
Since your team’s successful 2019 prototype launch, a plethora of developments have unfolded.
By securing Enterprise Capital in 2020, our team was empowered to design and build its inaugural manufacturing-focused consulting prototype. We also leased our premises in West Melbourne and commenced work on our meeting facility. Despite the obstacles posed by the COVID-19 pandemic, our team successfully sourced and inspected all key prototype components in 2021, culminating in a successful capital raise that combined a government grant, loan, and a favorable first road test.
As of 2022, we’ve accelerated progress by building and refining two successive prototypes. Through rigorous on-road testing, as well as attendance at industry events and customer gatherings nationwide, one manufacturer has honed its product while the other has leveraged ABS Improvement with Bosch Australia and ADR Authorities Compliance, marking a critical milestone preceding pilot production and initial customer deliveries.
The Savic C-Sequence has undergone significant refinements in its design and engineering, incorporating cutting-edge technologies to enhance performance, efficiency, and overall user experience.
Significant changes have taken place over the past few years.
The battery pack’s design has undergone a comprehensive redesign. By 2019, our predictions had hinted at pouch cells’ potential to be game-changing; nonetheless, we struggled to align the design, provider, and pricing targets accurately. This innovative design prioritized long-term durability and sustainability. We successfully transitioned to a prismatic cell architecture and revamped our supplier network, overcoming initial hurdles to achieve a high-quality battery solution for our e-bikes.
After navigating a thorough selection process for our battery pack, we also invested considerable time and effort into finding the ideal motor provider and constructing a value-driven partnership. Despite its troubled reputation, we ultimately found ourselves on that very same street. Persistence pays!
Both the 2019 and 2020 prototypes featured robust welded metal frames. In larger industries, this approach proves prudent due to the numerous benefits it confers on a company’s bottom line and operational efficiency. While metal frames present a viable option, their production demands substantial investments in welding jigs and fixtures, rendering them prohibitively expensive for emerging startups.
While attempting to reduce costs by employing fewer fixtures or jigs may seem appealing, a crucial trade-off is the compromised tolerance that can result in inferior quality for the rear hub. We gained a tremendous amount of knowledge throughout the process, ultimately redesigning every aspect to enable casting from aluminum. Before fabricating parts that fit seamlessly on a motorbike, a thorough machining process is required, not to mention a series of steps preceding the application of coatings. Regardless of whether it’s portrayed, powder-coated, or anodized. The machining process is actually what enables drill bits and faucets to precisely create all the holes within a product, ensuring exceptional accuracy. The entire course of action can be environmentally friendly enough to align with our company’s budget constraints. To underscore the sustainability benefits of aluminum, highlighting its recyclability and profitable nature, in alignment with our organization’s core values.
The C-Sequence fashions, comprising of Class-A to Class-C, diverge in terms of fabric types, with Class-A featuring luxurious materials like silk and cashmere, whereas Class-B employs high-quality synthetic fabrics and Class-C prioritizes affordability through the use of polyester blends.
The Café Racer sequence is available in two distinct variants: the high-performance Alpha and the urban-focused Delta. While seemingly alike, a crucial disparity exists between these units, primarily driven by their distinct battery sizes, resulting in varying power capacities and price points.
PRICE $26,990 AUD experience away POWER – 60KW TORQUE – 200NM HORSEPOWER – 80HP CHARGE – 4.5 HOURS 0-100 km/h – 3.5s RANGE: – 200+ KM *mixed |
Price: $19,990 AUD – Experience the World Away POWER – 40KW TORQUE – 140NM HORSEPOWER – 54HP CHARGE – 3.8 HOURS 0-100 km/h – 4.5s RANGE – 150KM + *mixed |
Mixed city and freeway driving combined with regenerative braking during urban stop-and-go traffic.
Journey away pricing includes all on-road costs and supplier fees, excluding additional options and transportation expenses.
As both Alpha and Delta undergo rigorous testing alongside simulations of real-world scenarios, varying energy levels, and suspension dynamics, we are cautiously optimistic that we will surpass our customers’ expectations; while conserving a realistic outlook for the immediate future.
We now offer a palette of four distinct colors for customers to choose from. Atomic Silver, Darkish Matter Black, Radiate Aluminium, boasting a brushed aluminium finish on the tank cowl and rear cowl, or opt for a cutting-edge Carbon Fibre option, featuring gloss carbon accents on the tank cowl, rear cowl, and belly pan, complemented by matte carbon elements on the front and rear fenders and belt cowl.
We offer two seating trim options, both available with either a dark-tan or black synthetic leather finish that is impressively durable. As we continue exploring sustainable leather alternatives for our bicycles, gear, and apparel, including innovative materials like mycelium and cactus-derived leathers.
Try out our extensive range of bikes and have fun exploring our innovative customized bike builder feature on our website.
Where are the Savic bikes being manufactured?
Our bicycles are conceived and refined in West Melbourne, with a global network of suppliers providing components from India, China, Europe, and Australia. Every motorcycle is meticulously hand-assembled from the ground up within our state-of-the-art meeting facility in West Melbourne. Our intention is to deliver the primary units of the C-series bicycles directly to clients through our Melbourne Savic Bikes showroom, which is scheduled to open later this year, or to their doorstep via our trusted transportation partners for interstate buyers.
We’re poised to expand our national reach by establishing boutique Savic Bikes dealerships across the country, complemented by a network of partner service centers. Our motorcycles’ 4G connectivity enables seamless remote updates and analysis, further streamlining our operations. Our skilled team of software developers has successfully enhanced our on-site linked rider experiences and will continue to build upon and refine these offerings, delivering remote support to clients from our Melbourne base.
The Savic motorcycle is manufactured using a combination of advanced technologies and traditional craftsmanship. Firstly, the company employs a unique modular design approach, which enables them to produce high-quality components that can be easily assembled into various models. This modularity also allows for greater flexibility in terms of production volumes and customization options.
Here’s the improved text:
The production process for each part of a C-series motorcycle is meticulously crafted across various components.
What unique value does Gravity Die Forged Aluminium bring to frames and enclosure applications?
High-quality, stress-free die-forged aluminium rims for a superior ride.
Prioritizing prompt attention: Freezing of the rear hub necessitates immediate action before rear axle bearing failure becomes an urgent concern, given the incredibly precise and tight tolerances at play.
Laser welding offers a reliable and efficient method for joining battery cell terminals to bus bars in electric vehicle applications. By utilizing high-powered lasers, this process ensures strong bonds that withstand the demands of repeated charge cycles and varying environmental conditions. In addition, laser welding eliminates the need for mechanical fasteners or adhesives, reducing potential failure points and increasing overall system reliability.
PCB Printing & Choosing – Totally Automated Electronics board manufacturing
Plastic parts are frequently created using injection moulding, a manufacturing process that involves injecting molten plastic into a mould to form the desired shape. The process begins with the design of the plastic part, which is typically made from a polymer or resin material. Once designed, the mould is created and the plastic material is melted and injected into the mould under high pressure.
Vacuum Forming – Seat Substrates
We’re investigating indigenous three-dimensional printing techniques for specific components.
Among the technological highlights of the C-Sequence are advanced materials used in its construction, such as high-strength steel and lightweight aluminum, which enable improved fuel efficiency while maintaining structural integrity.
The ruggedly dependable belt pushes forward with unwavering steadfastness, its solid construction ensuring a tranquil and maintenance-friendly performance.
The C-Series motorbike’s entrance pulley aligns concentrically with the swingarm pivot, thereby rendering a tensioner pulley unnecessary for the belt. The instrument cluster & software program and linked to a rider expertise with over-the-air diagnostics and updates. Our bespoke in-house development of the entrance suspension ensures a unique fit for the C-Series, with proprietary designs at both front and rear tailored to meet specific requirements.
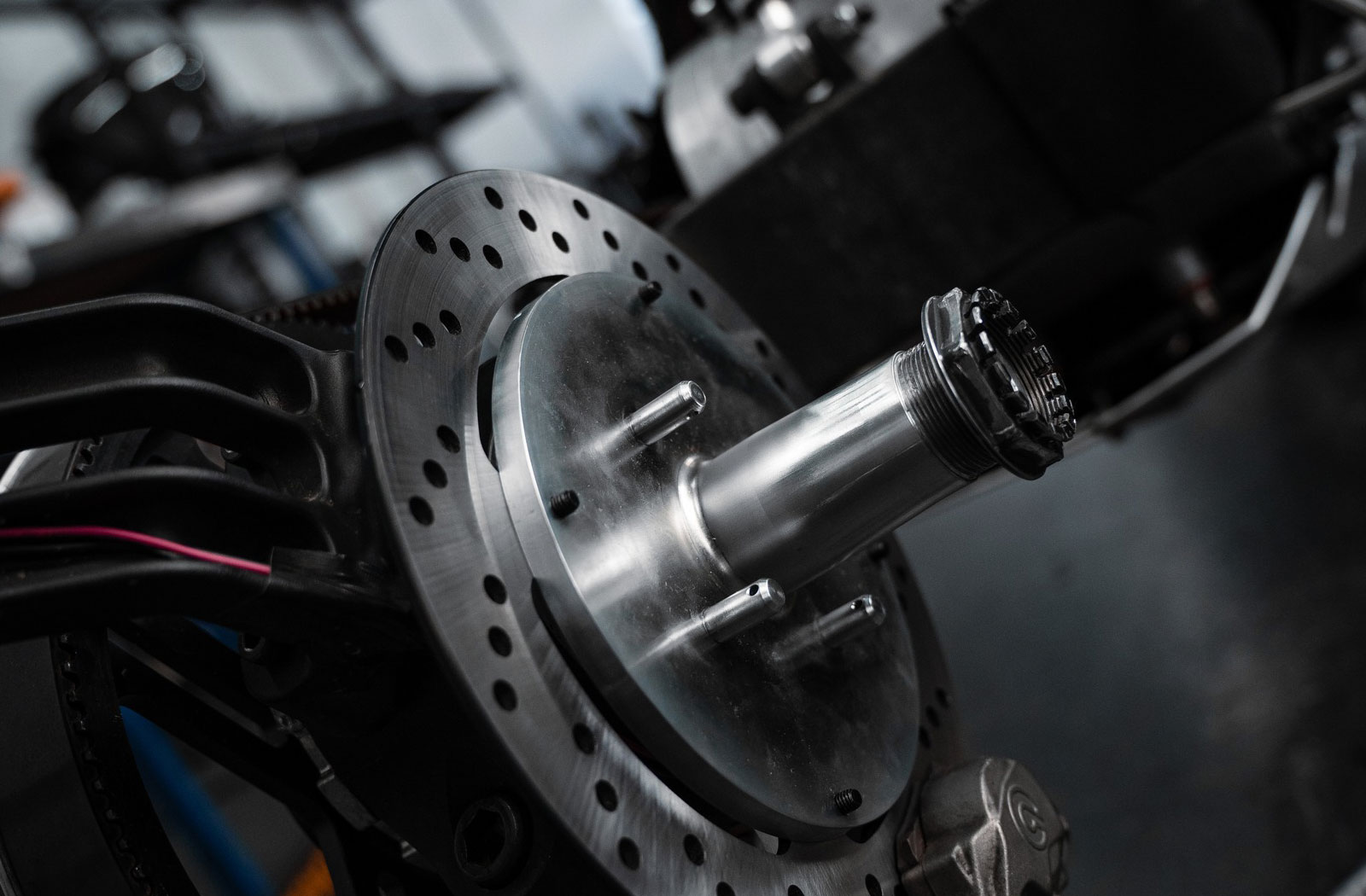
Navigating the complexities of homologation and registration proved to be a significant hurdle in our project’s timeline.
The engineering team made a Herculean effort to navigate the Advanced Braking System (ABS) growth with Bosch Australia. The course was both intense and crucial, ultimately yielding a fantastic outcome. That marked a significant milestone for us, allowing us to have a great time in September 2022.
Since then, we’ve navigated the ADR compliance process with relative ease, thanks to our Australian Design Guidelines software. Now, we’re eagerly awaiting the final green light from the federal government, which will enable us to register our vehicle on the road once the necessary paperwork is in place and approved. In light of recent developments, we are compelled to submit our concerns regarding the outdated framework, which is long overdue for a comprehensive review, alongside submissions from various Australian electric vehicle manufacturers, in response to the National Electric Vehicle Strategy’s latest paper.
Savic aims to begin delivering vehicles to its inaugural customers within the next 12-18 months.
Although our initial shipments require ADR clearance, we’re optimistic that we’ll be able to deliver some by year-end. We plan to place our initial order for serial manufacturing components in January 2023 to ensure a March delivery date for our inaugural 25 customers. Throughout our company’s timeline, numerous clients have developed a profound connection with us, one that has evolved organically over time as we’ve navigated the journey to this pivotal moment in Australian history.
To date, we’ve surpassed 235 orders across just two production cycles, and we’re nearly sold out from our second run with a mere 15 build slots still available? As we look ahead to launching our second manufacturing run in late Q2 2023, it’s an honour and a testament to the dedication of our workforce that we’re able to achieve this milestone. We proactively inform our valued clients of any updates to project timelines or key milestones, and we’re eager to celebrate our achievements with them. We’ve successfully created an innovative product that people are eager to own and experience, and we can’t wait to get it out into the world.
To stay informed about Savic’s ongoing developments or secure one of the last remaining C-series electric cafe racers from their limited production run, visit Savic’s website directly.