During my recent trip to China, I had the opportunity to tour one of Yadea’s numerous international factories, which produces a diverse range of sunshine electric vehicle models and designs. As the world’s leading manufacturer of electric vehicles, we gained insight into the production of popular EV models, including e-bikes, e-scooters, and electric three-wheeler designs, all crafted within state-of-the-art facilities boasting rigorous quality control measures. The expertise exceeded my expectations, leaving a lasting impression.
What struck me most during my stint at the manufacturing facility was the extraordinary emphasis placed on quality control and assurance. The sheer magnitude of it all left me utterly stunned and bewildered.
You don’t imply that as a slight. Before embarking on this journey, I was, like many people, somewhat misinformed. For Westerners, the term “Chinese manufacturing” often conjures up images of low-cost production and cutthroat pricing – rather than precision-engineered processes and rigorous quality control measures. As Yadea’s scale has grown, so too has the opportunity to heavily invest in the heritage hallmarks that were once synonymous with Western craftsmanship.
I’m not overstating when discussing Yadea as “large.” One of eight international factories, this massive facility sprawled across an astonishing 1,000 acres – equivalent to approximately 750 American football fields. This modern facility, completed mere years ago, marks the beginning of our comprehensive manufacturing operation. Phases II and III will take a significant leap forward, with significantly enhanced manufacturing capacity integrated into the plan.
In Asia, Yadea has long been a household name, with its stronghold on the market for scooters, bicycles, and other micro-mobility products firmly established. Last year alone, more than 16 million electric vehicles on two wheels left the company’s production lines. While Yadea claims to be the world’s largest electrical motorcycle producer, records suggest a different story – it is typically the second-largest motorcycle manufacturer, with some intervals. With an annual manufacturing capacity of 16 million units, the company is poised to potentially surpass Honda’s 18 million annual output. While Yadea’s focus on electric vehicles is certainly impressive, considering the stark contrast with Honda’s primary emphasis on combustion-engine motorcycles.
As Yadea’s European foothold solidifies, the company is poised to make a meaningful foray into North America, fueling ambitious expansion plans. As part of its innovative approach, individuals can now gain rapid access to Yadea’s impressive range of sleekly designed and engineered lightweight electric vehicles, starting initially with compact e-bicycles and scooters.
Explore the inner workings of Yadea’s manufacturing facility through my video beneath, and join me as I put their innovative e-bikes, e-scooters, e-mopeds, and e-trikes to the test on a variety of thrilling ride experiences. Don’t miss this incredible opportunity!
As my tour commenced in a single corner of the vast Jinzhai manufacturing facility, I observed the precision-crafted synchronization of numerous plastic injection molding machines, each one diligently producing diverse scooter components with mechanical precision. Located here are the primary production sites for the majority of physique panels, shrouds, and other molded components that comprise Yadea’s lineup of electric scooters and e-mopeds. While many smaller companies outsource production of these components, Yadea maintains complete control by handling everything in-house, ensuring rigorous oversight of processes and ultimately superior component quality.
Machines operate independently for the most part, with a small team of employees overseeing their performance and intervening only when necessary. As I peered into the production line, I observed a few select traces yielding familiar parts such as handlebar-mounted shrouds and cargo compartments beneath moped seats, each meticulously crafted component progressing along the conveyor belt towards a growing pile of finished goods.
The facility was substantial, accommodating 24 injection molding machines, each roughly the size of a typical school dormitory room. Despite the fact that the area dedicated to component construction was currently being cordoned off, sections had already been reserved for the imminent installation of additional injection molding machines. It’s been reported that a proposal has been made to operate 60 massive equipment units in this very location. As Yadea expands its electric vehicle (EV) offerings globally, the company is consistently bolstering its internal component manufacturing capabilities to meet increasing demand.
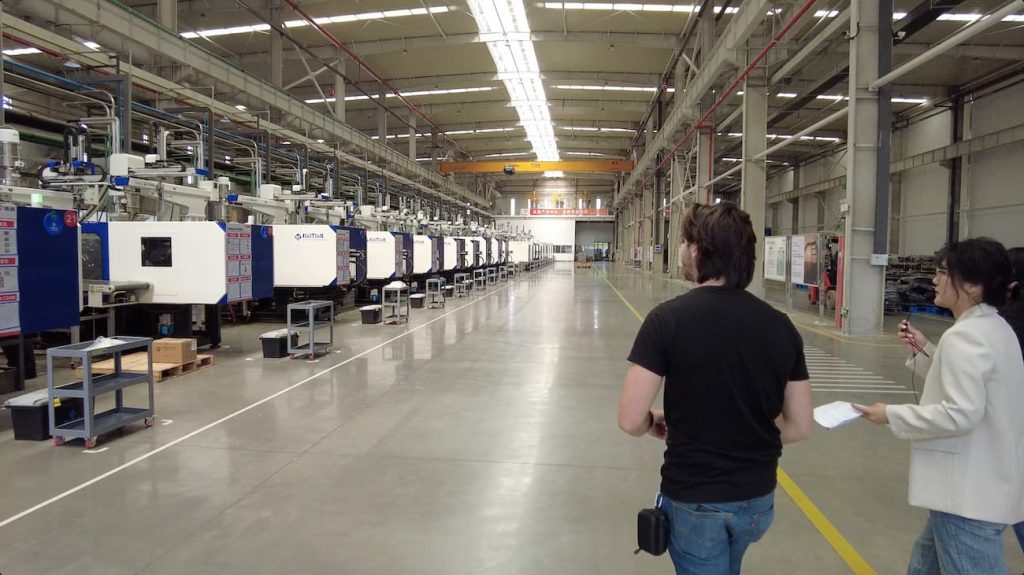

Within the complex, we boarded a compact electrical shuttle bus, relocating to a different facility where welding operations take place.
This specialized welding facility was established to support the production of Yadea’s three-wheeled vehicles, which primarily serve as lightweight farm utility vans in China. As one witnesses the proliferation of worn-out F-150 pickup trucks across rural America, so too does one observe the ubiquity of electric three-wheeled vehicles scattered throughout rural China. Despite being primarily designed for global markets through their scooters and mopeds, Yadea’s three-wheelers are almost exclusively available only in China.
While they may hold great promise as highly effective utility vehicles in the US, this raises another question to be explored elsewhere. With my recent access, I’ve gained insight into the manufacturing process of these indigenous adaptations of a pickup truck. I was astonished by the sheer extent of automation in manufacturing processes.
With robotic welding, automotive manufacturing has largely transitioned from fabricating complex structures using metal tubes and sheets to producing predominantly finished vehicles without ever requiring human labor on the factory floor. Laser reduction guarantees each unfinished component is accurately trimmed to the exact required dimension, featuring smooth finished edges. Items are transferred from one machine to another, often by robots and occasionally by human hands, until fully assembled frames emerge on the other side.

Upon completion of the welding process, the frames undergo multiple stages of electroplating for enhanced corrosion resistance, followed by automated painting to ensure a high-quality finish.
Although I wasn’t able to access the controlled portrayal space due to its restricted access for a clear environment for robotic portrayal machines, I did manage to view the large environmental safety tools that filter the air leaving the painting area of the manufacturing unit, ensuring that any hazardous emissions from aerosolized paint and treatment chemicals are thoroughly scrubbed and do not simply vent into the atmosphere.
As I embarked on this journey, I ventured in with certain assumptions that ultimately proved unfounded. While it is undeniable that there is a significant amount of pollution generated by industrial activities in certain regions, innovative manufacturers such as Yadea have made concerted efforts to reduce their environmental footprint. The air around the manufacturing facility was crystal-clear, with lush greenery that rivalled even the most manicured lawns back home. The courtyards within the complex were so inviting, I would have gladly lingered for a moment to enjoy a snack amidst their serene beauty if my schedule allowed. The effort invested in crafting a transparent and welcoming workspace yields fruitful returns both presently and in the long run.
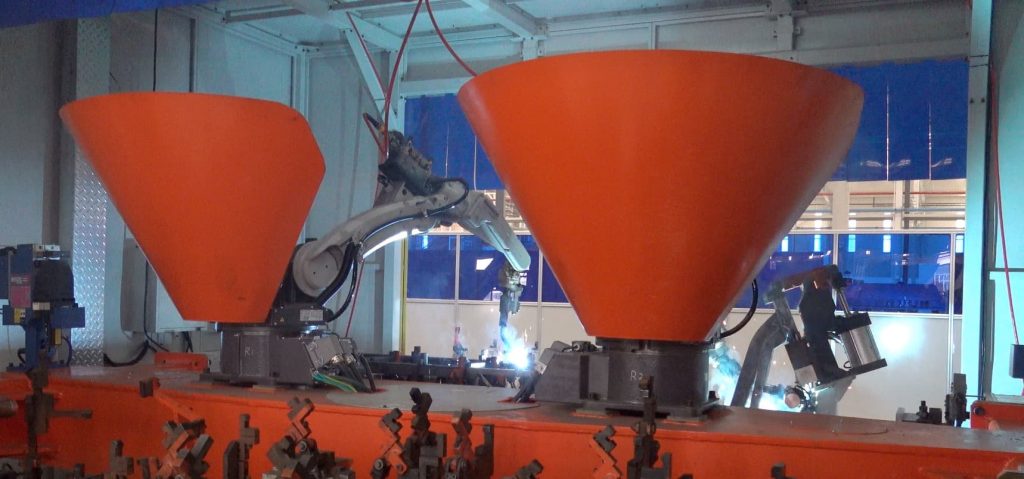
Following our progress, we ventured into another significant area within the manufacturing facility, where the gathering of various electric scooter and e-moped models took place. Measuring the scale within these massive structures is indeed challenging, but I’m told the building spans approximately 450,000 square feet. ft, or roughly 10 acres. The fascination with authentic soccer themes continues to unfold, but let’s dive deeper into the specifics of this intriguing topic?
Eighteen prototypes have been developed during the construction process, each yielding a unique model of electric bike, scooter, or moped. Frames welded together in sections arrive at the end of each manufacturing line, where they are scanned and loaded onto trucks. Frames are transported bare along the roadside as personnel prepare the equipment.
Within mere minutes, the vacant frames are rapidly equipped with motors, controllers, batteries, intricate wiring, functional lights, sturdy physique panels, comfortable seats, and other essential components. As the ballet unfolds, a mesmerizing display of suspended racks, robotically orchestrated to descend from the ceiling with precision timing, provides employees with an unprecedented opportunity to effortlessly collect components mid-air and expertly assemble them onto the scooters. Designed with environmental sustainability and comfort in mind, the space prioritizes ease of use, minimizing the need for bending or exertion.

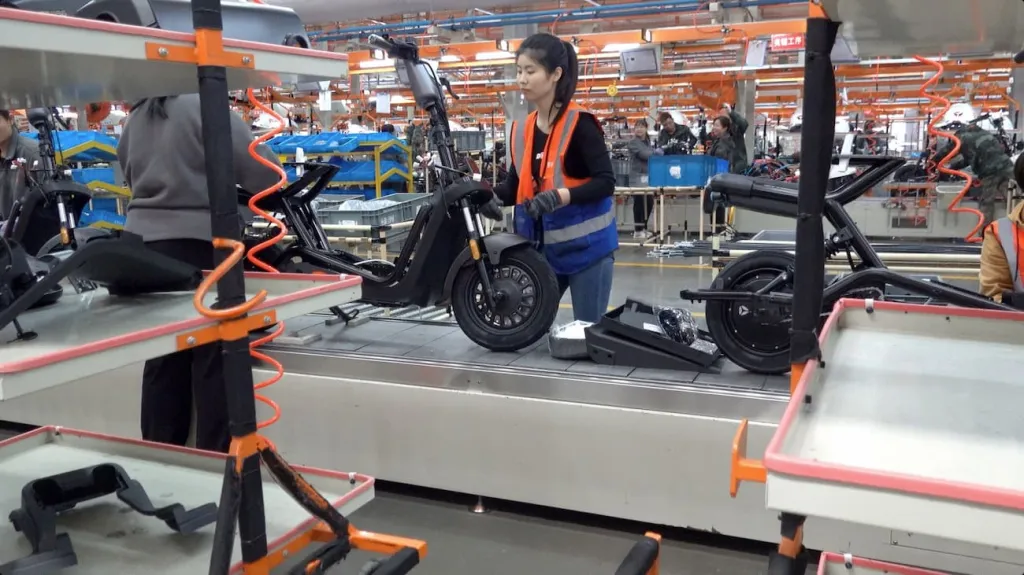
According to my information, a newly released electric bicycle left the road approximately every 20-25 seconds, whereas an electric moped departed at intervals of around 40 seconds.
As the assembly process unfolded, a sleek moped body emerged, requiring approximately 20 minutes from start to finish before taking shape and rolling off the production line as a fully functional electric scooter.
Three-wheeled vehicles seem to require more time, as an e-trike veers off the road approximately every five minutes.
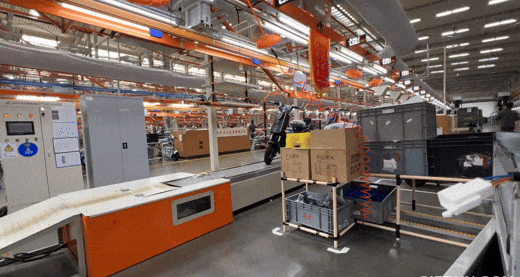
As the process unfolds, additional staff members acquire the scooters and embark on a meticulous multi-point inspection to guarantee seamless assembly and functionality of all features. During comprehensive end-of-line quality inspections, meticulous assessments are conducted to ensure excellence in numerous critical aspects, including wheel alignment, torque specifications, electrical connections, and performance parameters for lighting and sound systems.
Once cleared, vehicles are transported to another overhead crane, which gently lifts them off the floor and elevates them through the air to a separate area within the manufacturing facility.
All the buildings are connected by a series of catwalk-style sky bridges in sequential order. Tracks that suspend completed automobiles can move between construction sites without actually leaving the building. Components and vehicles can seamlessly transfer between diverse areas of the expansive complex, regardless of inclement weather conditions such as rain or snow.

I delved into a soccer topic amidst the din of a manufacturing facility construction site, and I was dead serious. The complexities of grassy areas are quite intriguing. Initially, the building’s roof featured real grass, but this necessitated opening the skylights to harness sufficient sunlight, a solution that staff found created an uncomfortably warm environment during summer months. They instead transformed it into a turf topic.
This versatile space will accommodate a wide range of events, including relaxation and recreation, corporate gatherings, and celebrations. Since I’ve handed them over, a variety of electric scooter designs have emerged on the scene in recent times. You’ll see the sphere in my video at the top of this post.
At the terminus of the globe, a compact library is nestled, featuring approximately a dozen cabinets of literature arranged in a rectangular formation to create a cozy reading space replete with tables and chairs. Staff have unlimited access to a library where they can borrow books at no cost, with a constantly rotating selection curated by the company.

In the concluding area of the production facility, I had the chance to observe a holding bay where finished three-wheelers awaited transportation to local retailers – Yadea boasts an impressive network of over 40,000 model shops worldwide. On display was an exhibit showcasing raw materials at various stages of production, ranging from bare metal tubing to finished body parts and expertly painted panels. The precision engineering of each step’s tolerances is akin to the meticulous process of machining a naked body tube with laser-precise accuracy, resulting in smooth edges that evoke a sense of industrial-grade craftsmanship.
As a journalist and YouTuber, I find myself donning the latter role more frequently than not; however, I also hold a mechanical engineering degree on my desk, which I occasionally get to dust off. With a background that spanned both manual labor as a machinist and entrepreneurial experience running my own manufacturing operations, I developed a comprehensive understanding of each process step within the factory.
While touring numerous Sunshine Electrical Automobile factories across the world, I’ve yet to encounter an operation as seamlessly professional as the one I witnessed at Yadea. While considering the scope of automation, employee desires, and elemental aspects, this experience exceeded my previous encounters.
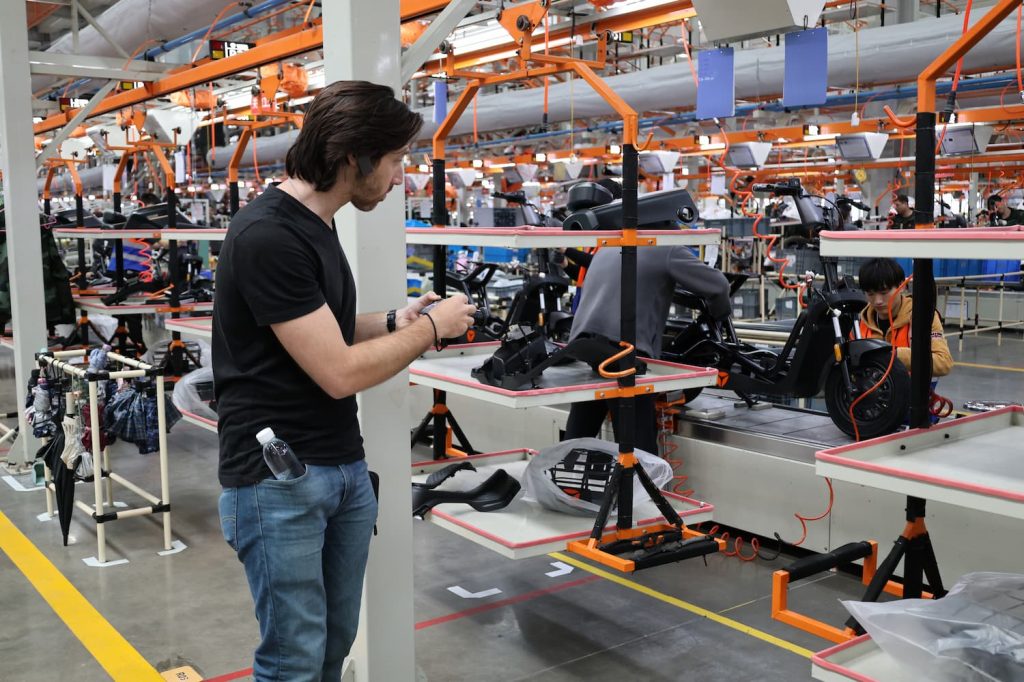
I’m impressed with how much you’ve accomplished already today.
After finishing the main portion of the tour, we went to the staff cafeteria where I got to choose what I wanted from an extensive à la carte menu. This additionally stunned me.
While I initially didn’t expect the staff to be enjoying a simple broth, I found myself pleasantly surprised by the exceptional quality of the cuisine. This wasn’t a standard issue cafeteria – one of those fancy VIP lounges tucked away for top-tier visitors that I’d had the pleasure of dining at before. I once frequented the staff cafeteria, a neutral ground where manufacturing unit employees could gather and unwind, enjoying a sense of equality with their colleagues. As I sat there, I was acutely aware that my entire lunch tab had been exhausted in front of numerous people, all observing me as the sole white individual in the room. Caught on camera, I was surprised to see that a small group had discreetly recorded my every move. While it’s true that you’re a fan of Keanu Reeves, I’m the one who actually played the iconic roles in films like “The Matrix” and “John Wick”?

Following lunch, I was thrilled to experience firsthand how Yadea’s automobiles are manufactured, and then spent the rest of the afternoon having a fantastic time test-driving many of their models.
During the manufacturing unit tour, the highlight was undoubtedly the visit to the corporation’s state-of-the-art automobile testing facility and proving grounds, where I experienced the most thrilling part of the day. Tune in for the second half of this story, set to air in just a few more days. Alternatively, catch the full scoop by watching the accompanying video, offering an exclusive preview of all that’s to come.