By optimizing the vehicle’s aerodynamics through the application of advanced computational fluid dynamics and wind tunnel testing, a reduction in drag coefficient can be achieved, resulting in a decrease in engine power required to maintain speed, thereby lowering carbon dioxide emissions by approximately 50%. Seems like a riddle, proper?
The pilot program, a collaboration between BMW Group Logistik and Trailer Dynamics, based in Germany, has successfully achieved this goal. I recently discussed this technology with Mo Köllner from BMW and Michael Nimtsch from Trailer Dynamics, both of whom were enthusiastic about its potential applications.
The answer lies in transforming a standard semi-truck trailer into an innovative solution. To achieve this, install a substantial battery pack with a capacity of up to 600 kWh within the trailer’s bed. This powerhouse then drives an electric-powered axle situated underneath the trailer, revolutionizing the way goods are transported. While not groundbreaking, e-trailers have indeed gained traction over time, with different models catering to diverse needs since their introduction several years ago. The technology still lingers in its early stages of development. The fundamental principle is straightforward. By integrating a battery-electric powertrain with a diesel tractor-trailer, you significantly reduce the fuel consumption of the diesel component in the hybrid system. You’ve developed a novel plug-in hybrid-electric heavy-duty vehicle configuration. Fairly simple, yeah?
What sets Trailer Dynamics’ response apart is its simplicity and ease of implementation – a truly “plug-and-play” solution. In reality, the corporation asserts that its electric trailers are designed to operate seamlessly with any truck that is physically capable of being connected to them. The e-trailer functions autonomously without relying on a trailer-to-truck connection. What sets Trailer Dynamics apart is that its product stands out from other e-trailer options in the market, as most of them necessitate real-time communication with the linked truck to facilitate smooth electric-assisted driving. BMW is currently testing TD’s response with its BMW Group Logistics fleet. s
TD achieves this precise control through its proprietary sensor pack, cleverly integrated into the kingpin of the trailer itself. The PC management model receives input from sensors monitoring various forces on the kingpin, converting this data into a decision regarding when and how much power to allocate to the electric motors within the axle. The system’s logic considers various types of personal property. When a trailer is cognizant that the truck has come to a halt and is about to initiate movement, it would exert tremendous kinetic energy to coax the truck into motion, as massive vehicles tend to consume fuel least efficiently when stationary. The outcome yields a substantial reduction in cost corresponding to the volume of diesel consumed. When the system detects a truck ascending, it will likely deploy electric assistance liberally to mitigate the effects of what would otherwise be a fuel-hungry scenario, thereby reducing the environmental impact and improving overall efficiency. On TD’s website, factors such as climate conditions, route topology, and site visitors are considered, but the extent to which they influence energy application by the trailer is unclear. To ensure seamless operations, the system can be set to automatically shut down when the battery capacity drops below a predetermined threshold, thereby guaranteeing a minimum level of cost containment at all times.
While the system itself is a significant component in electric vehicles, its sheer robustness stems directly from the demands placed upon it by passenger electric cars. The company employs battery packs in capacities of either 400 kilowatt-hours (kWh) or 600 kWh, with the latter option proving particularly captivating for many of its prospective clients, including the highly anticipated introduction of a 200 kWh unit later on. As a consequence of economies of scale, longer routes appear to reward investments in larger batteries more effectively. The electrical motor unit boasts an impressive output of 580 kW (777 hp), but it’s the astonishing 13,000 nm of torque that truly sets it apart. Charging can occur at a remarkably rapid pace, thanks to the vehicle’s 800-volt architecture, which enables 44 kW of alternating current (AC) and up to 350 kW of direct current (DC) fast charging. As one considers the considerable weights involved, the supersized figures on display become increasingly logical – BMW is rigorously testing TD’s trailers, capable of hauling payloads of up to 16 metric tonnes, equivalent to an astonishing 35,000 kilograms. In recent times, BMW has leveraged electric trucks to transport electronic components for its passenger vehicles.
According to early results, BMW has observed a significant reduction in gasoline consumption on various long-haul routes being tested, resulting in lower emissions along those routes. Additionally, even on shorter routes, the company reports an impressive 45% or greater decrease in fuel costs. As a direct result of BMW’s adoption of 100% carbon-neutral sources for recharging the trailer batteries, the company projects a reduction in CO2 emissions from its fleet of up to 120 tonnes per year with each e-trailer. By utilizing trailers efficiently, the equivalent environmental impact is comparable to removing approximately 60 typical ICE vehicles from the road, resulting in a reduction of around 5 tonnes of CO2 emissions annually. It’s indeed exhausting to exaggerate the monumental fuel consumption of a genuine large truck.
BMW has been conducting trials of its Tactical Decision-making (TD) system in conjunction with electric vehicles, where it effectively functions as a range extender for the latter. BMW claims that the range of its electric truck can be extended by a factor of 2-3 times, depending on the specific truck, payload and route, potentially opening up new opportunities for using battery-electric vehicle (BEV) tractor units. BMW successfully tested its electric truck capabilities by partnering with Volvo and utilizing an unidentified e-truck, along with a TD Mega Trailer, to travel more than 600 kilometers (373 miles) without the need for recharging.
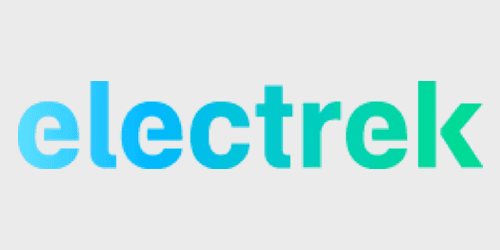
If technological advancements continue to propel the automotive industry forward at its current pace, a future where diesel-powered vehicles are all but extinct is not entirely far-fetched. Despite being considered long-lasting assets, the design principle of vehicles suggests that internal combustion engine (ICE) trucks will persist for a considerable period longer than their passenger car counterparts. As e-trailers like those developed by Trailer Dynamics gain traction in reducing trucking fuel consumption at a large scale, we can still achieve a tangible positive impact on emissions throughout this transition process. As electric vehicles’ and internal combustion engine tractors benefit from this technology in distinct ways, arguably with the former deriving greater advantage, this scenario lends itself to a hybrid system transition making more sense. No modifications are necessary to render these trailers obsolete in a post-ICE era.
With BMW’s reliance on its unique “mega trailer” configuration for a substantial portion of its transportation fleet, the electric vehicle (EV) truck options are significantly constrained, presenting an added challenge in this regard. By employing TD’s mega trailer response as a spread extender, you’ll discover a clever solution to overcome this challenge effectively. Mega trailers are a high-capacity trailer class specifically designed for widespread use within the European Union, where they remain extremely popular.
The trailers designed to maximize space necessitate a unique type of truck chassis featuring an exceptionally low deck height for towing purposes. Unfortunately, this configuration leaves limited or no room for a battery installation.
As for the daunting task of integrating a substantial battery into the rear compartment of an already burdened trailer? They’re not nonexistent. In terms of transport efficiency, BMW’s TD options excel when utilizing containers in their fully maximized “cube-out” configurations – i.e., occupying the maximum volume possible, rather than exceeding weight limits. And indeed, the battery consumes some available space for cargo storage. As the technology behind TD’s weight discount system continues to advance and refine itself, it becomes increasingly likely that even heavier payloads will become feasible in the future. Human behavior is another significant concern to consider. Suppose a tractor operator continues to drive recklessly, oblivious to the consequences of their hasty actions. By optimizing driving habits and adapting to varying conditions, it is possible to significantly reduce fuel expenditures, with BMW reporting that gas consumption can vary by up to 20% depending on the driver. BMW posits that electrification of trailers will substantially reduce fleet operating costs, potentially justifying the initial investment in these advanced technologies.
TD proposes leveraging its technology to enhance on-highway safety for tractor-trailers by harnessing power or engine braking force to maintain stability, potentially preventing accidents like jackknifing. Currently, the company is just starting out, with seven operational trailers and an additional eighth having recently been delivered.
While efforts to reduce carbon footprints from personal vehicles can yield tangible benefits for global CO2 emissions, it’s equally crucial that we consider the far more substantial effects of freight transportation on climate change. According to the International Energy Agency (IEA), highway freight is responsible for approximately 30% of international transportation emissions, a significant contribution that trails only passenger automobiles in magnitude. Air and sea transportation collectively account for a mere 10% of global emissions annually. The rail industry’s growth rate remains stagnant, hovering at just 1%.