Aito, a cutting-edge Chinese language model, has ventured into the realm of diecasting, marking a significant milestone in its development. In 2021, Huawei and Seres partnered to launch the first model under their Concord Clever Mobility Alliance (HIMA) joint venture, where Seres built the vehicle while Huawei provided full-stack intelligent automotive solutions. Following the conclusion of last month’s experiences, Seres has successfully transitioned to die-casting for production of its Aito M9 model, reportedly enhancing manufacturing capacity through this move.
Serious efforts are being made to utilize a Wencan IDRA9800T unit, a premier 10,000-ton class massive die-casting machine. The setup of the unit commenced in February. While unconfirmed, the manufacturer appears to be producing one-piece diecast components specifically designed for the Aito M9’s rear physique, with a high likelihood of these parts being intended for the chassis rather than any other aspect of the vehicle. This implies that a significant reduction occurs in component diversity, amounting to nearly an 80% decrease, while solder joint variability is diminished by approximately 1,440 instances. Seres asserts that its technology optimizes the seamless integration of diecast parts, resulting in a substantial 23% boost to torsional stiffness. The widespread adoption of this technology significantly simplifies production processes, resulting in a substantial boost to manufacturing efficiency, while also enhancing vehicle durability and energy-conserving capabilities.
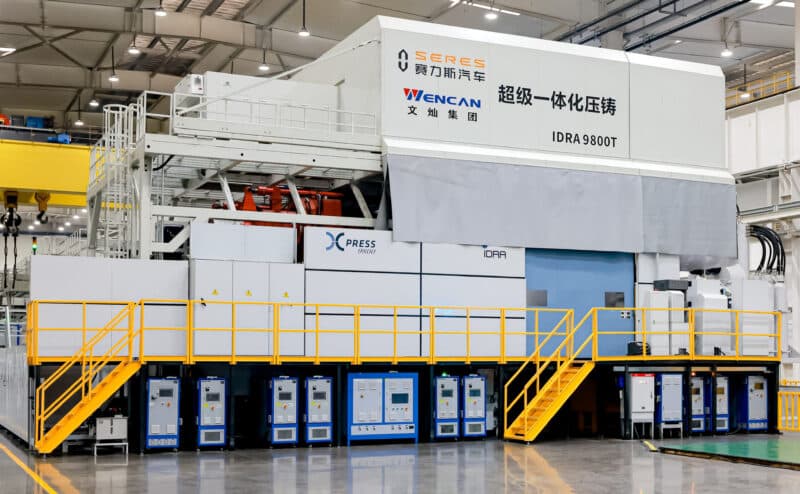
The die-casting machine will allegedly be employed in the upcoming Aito M8 production process, with the M8 serving as a five-passenger variant of its seven-seat counterpart, the M9. With demand exceeding 100,000 units, the Aito M9 has proven to be an overwhelmingly popular product. Deliveries began earlier this year, with a little more than half completed to date. Seres anticipates that the die-casting machine will enable it to exceed its monthly delivery targets of 15,000 units.
Gigantic-scale die-casting technology was initially pioneered by Tesla, which they dubbed the Giga Press. Since then, numerous Chinese manufacturers have developed these machines to streamline production, reduce costs, and boost stiffness, thereby enhancing the safety of vehicles. Xpeng currently employs a 12,000-ton press machine to manufacture its X9 MPV model, while also leveraging die-casting technology across various other models. Nio also leverages this manufacturing technique, having been previously featured on our platform alongside Xiaomi’s innovative approach two months ago when we covered the latter’s use of die-casting for the rear floor assembly of the Xiaomi SU7. Xiaomi’s 9100T machine achieves a groundbreaking feat by condensing 72 previously labor-intensive components, requiring stamping and welding, into a single, elegantly streamlined die-cast half – a production marvel that can be accomplished in a mere 100 seconds.
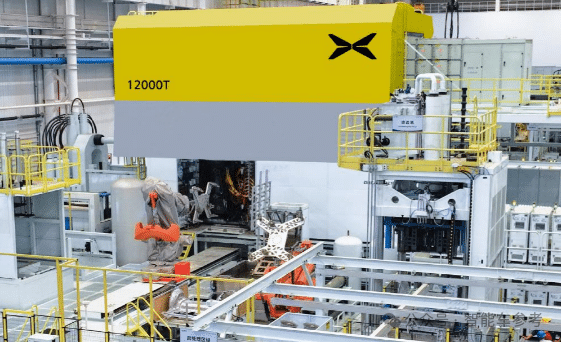
Sources: Quick Know-how, Quick Know-how,